Concrete is a durable material that’s used in many parts of your home, but it’s not indestructible. Damaged concrete surfaces must be repaired in a timely manner to ensure safety and minimize future costs.
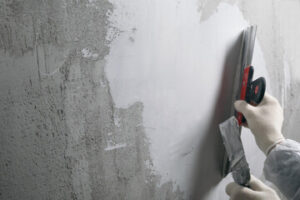
There are several methods for repairing concrete surfaces. The best method for a specific surface depends on the type of damage and its cause. Contact Concrete Repair Bismarck for professional help.
Cracks are inevitable in concrete structures and can occur for a number of reasons. Non-structural cracks usually don’t weaken the structure but may be indicative of other underlying issues that need to be addressed, such as soil instability or moisture intrusion. The sooner these problems are addressed, the less likely it is that the cracks will worsen.
Concrete crack repair methods can vary depending on the type of crack and underlying cause. For non-structural surface cracks, a vinyl concrete patching compound or filler can be used to seal and smooth the cracked area. For deeper cracks, epoxy injection can provide a permanent solution to both the appearance and structural integrity of concrete structures.
For structural cracks, it is important to chisel out the crack and clean the area prior to using a repair product. This will allow the crack repair material to better adhere to the concrete. It is also a good idea to use a bonding adhesive prior to application of the repair product. This will improve adhesion and ensure that the concrete crack filler or sealant will hold.
Crazing and crusting cracks are common in concrete floors that have recently been stamped, poured or cured. These shallow, fine cracks resemble spider webs and are caused by rapid evaporation of moisture on the surface of the concrete during curing or stamping. While these cracks don’t typically affect the structural integrity of the concrete, they do impact aesthetics and can lead to moisture ingress.
Expansion and shrinkage cracks occur in structures that are loaded more than their design capacity, often due to heavy traffic or machinery. These cracks can be corrected by installing expansion joints or high-strength epoxy injection to relieve the stress on the concrete.
Loose Concrete
Concrete is one of the most durable building materials available, but that doesn’t mean it’s impervious to damage. The constant exposure of concrete surfaces to harsh weather, heavy foot and vehicle traffic, or chemical damage can wear away at the structure and lead to surface issues such as cracks and spalling. Often, these surface problems also indicate the need for structural repairs. Repairing the problem at its source can prevent further deterioration and help to extend the life of the surface.
Inspect concrete for any signs of deterioration or damage and take action as soon as possible. The longer a problem is left unrepaired, the more difficult and costly it will be to fix.
Surface deterioration and damage can be caused by a variety of factors including age, freeze-thaw cycles, poor installation practices, rock or salt use, and exposure to chemicals. Typically, the damaged area will have a rough texture and may look pitted or flaked. The surface may also be discolored and exhibit efflorescence, which is a white or yellowish deposit that indicates the presence of water in the concrete.
Loose concrete can be repaired by removing the loose material and repairing the exposed aggregate with a repair mortar mix. It’s important to make sure the repair area is properly prepared and that the concrete mix or resurfacer is matched to the original surface for the best result.
It’s also a good idea to provide ample curing and drying time for the new surface, especially in colder climate conditions. This will ensure the proper bond and long-lasting performance of the repair.
Just like a dentist, every successful construction project begins with proper preparation. While anyone can rent a shabby office and grab a tool box, the skills of the contractor determine how well a job is performed. Similarly, the tools and products used for commercial concrete repair are critical to a project’s success. With a bit of time and effort, contractors can maximize their results and minimize the need for future repairs by following these concrete repair tips.
Scaling
Deterioration of concrete structures occurs from a variety of causes, including moisture, chemical attack and normal wear. Many of these problems can be corrected or mitigated by evaluating the structure’s condition and taking corrective action at the right time.
Identifying the problem and classifying it as major or minor is important before starting any repair. Then a qualified person can determine what type of repair is needed. This person can also evaluate if the structure will reach its design life through the use of repair methods.
Surface repairs typically involve a patching material that fills in the damage on the surface of the concrete. This is commonly used for spalling, small pock marks in the surface and surface wear.
The first step is to clean the damaged area and remove any loose debris. This can be done with a pressure washer or a sledgehammer and chisel. This is an important step to make sure that the area is sound and the underlying concrete is still structurally strong.
The next step is to profile the surface of the concrete. This creates a rougher surface texture and improves the mechanical bond between the existing concrete and the repair material. This can be achieved through shot blasting, acid etching or manual means like hammer and chisel. It is recommended that the profile be consistent across the entire damaged area to achieve a consistent result.
Once the surface is clean, it is necessary to moisten the mating surfaces of the existing concrete and the new repair materials to help hydrate the cement and ensure that they will bond. This will also reduce the tendency of the new concrete to shrink and loosen as it cures.
The repair materials themselves must be mixed according to the manufacturer’s recommendations and placed under proper conditions. For example, if the repair is using an epoxy-bonded product, it is recommended that the matrix be kept in saturated surface dry (SSD) condition. This is because epoxy products rely on the presence of moisture to hydrate and set. Concrete repair products that do not require epoxy bonds should be applied while the substrate is moist and then covered with a damp burlap sheet or plastic to prevent the new concrete from pulling moisture away from the substrate and weakening it.
Water Damage
Concrete is tough and durable, but even it isn’t immune to damage from moisture. If left unattended, moisture can weaken the structural integrity of concrete surfaces, resulting in large cracks and costly replacement projects. However, with the right knowledge and tools, repairing concrete is a relatively simple process. The key to a successful repair is recognizing the signs of water damage and taking prompt action.
Moisture-related damage to concrete often shows up as small pock marks that expose the aggregate underneath. This is known as scaling and it can be a good indicator of moisture penetration. If you notice any scaled areas, it’s a good idea to call for professional concrete repairs to avoid more serious problems down the road.
Other moisture-related signs of damage to concrete include discoloration and efflorescence. Discoloration is usually the result of salt deposits that are carried to the surface by condensation from moisture in the air. Efflorescence is a chalky white residue that appears on the surface of concrete. Both of these issues are signs of moisture intrusion and can be caused by a variety of factors, including freezing temperatures and excessive moisture.
Fortunately, many of these issues can be repaired by applying a cement patch or overlay. It is important to use high-quality products that are designed for concrete repair and follow all instructions carefully. Cutting corners or rushing can lead to recurring problems.
It is also important to consider the long-term consequences of a repair project before starting. A repair should take into account the desired appearance, functionality, and durability of the concrete. A concrete coating or overlay may be a better option for an aesthetic fix, while a full-scale replacement of a damaged area is appropriate for a structural problem that could compromise the safety and stability of your home.